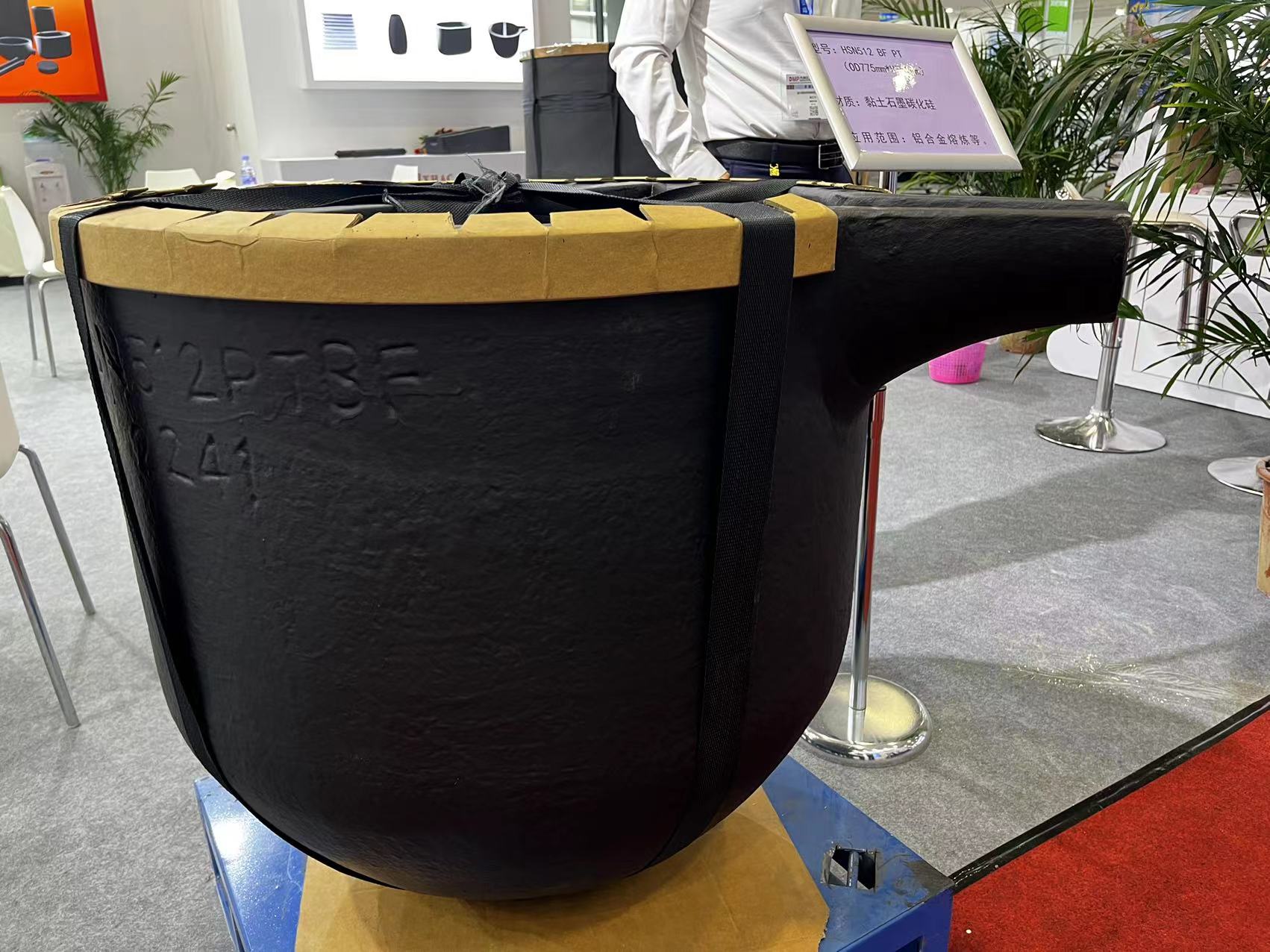
În lumea metalurgiei și a științei materialelor,creuzetuleste un instrument esențial pentru topirea și turnarea metalelor. Printre diferitele tipuri de creuzete, creuzetele de carbură de siliciu de grafit (SIC) ies în evidență pentru proprietățile lor excepționale, cum ar fi conductivitatea termică ridicată, rezistența excelentă la șoc termic și stabilitatea chimică superioară. În acest articol, vom aprofunda rețeta pentru creuzetele de grafit SIC și vom explora modul în care compoziția lor contribuie la performanța lor remarcabilă în aplicațiile de temperatură ridicată.
Ingredientele de bază
Componentele primare ale creuzetelor de grafit SIC sunt grafitul de fulgi și carbura de siliciu. Grafitul de fulgi, care constituie de obicei 40% -50% din creuzet, oferă o conductivitate termică și lubrifiere excelentă, care ajută la eliberarea ușoară a metalului turnat. Carbura de siliciu, care constituie 20% -50% din creuzet, este responsabilă pentru rezistența la șoc termică ridicată a creuzetului și stabilitatea chimică la temperaturi ridicate.
Componente suplimentare pentru performanțe îmbunătățite
Pentru a îmbunătăți în continuare performanța la temperatură ridicată și stabilitatea chimică a creuzetului, se adaugă componente suplimentare la rețetă:
- Pulbere elementară de siliciu (4%-10%): îmbunătățește rezistența la temperatură ridicată și rezistența la oxidare a creuzetului.
- Pulbere de carbură de bor (1%-5%): crește stabilitatea chimică și rezistența la metale corozive.
- Argila (5%-15%): acționează ca un liant și îmbunătățește rezistența mecanică și stabilitatea termică a creuzetului.
- Liant de termozetare (5%-10%): ajută la legarea tuturor componentelor împreună pentru a forma o structură coezivă.
Formula de înaltă calitate
Pentru aplicațiile care solicită performanțe și mai mari, este utilizată o formulă de creuzet de grafit de înaltă calitate. Această formulă cuprinde 98% particule de grafit, 2% oxid de calciu, 1% oxid de zirconiu, 1% acid boric, 1% silicat de sodiu și 1% silicat de aluminiu. Aceste ingrediente suplimentare asigură o rezistență inegalabilă la temperaturi ridicate și medii chimice agresive.
Proces de fabricație
Pregătirea creuzetelor de grafit SIC implică un proces meticulos. Inițial, grafitul de fulgi și carbura de siliciu sunt amestecate bine. Apoi, la amestec se adaugă pulbere de siliciu elementar, pulbere de carbură de bor, argilă și liant termozetting. Amestecul este apoi apăsat în formă folosind o mașină de presare rece. În cele din urmă, creuzetele formate sunt sinterizate într-un cuptor cu temperaturi ridicate pentru a-și îmbunătăți rezistența mecanică și stabilitatea termică.
Aplicații și avantaje
Cruciabilele de grafit SIC sunt utilizate pe scară largă în industria metalurgică pentru topirea și turnarea metalelor, cum ar fi fier, oțel, cupru și aluminiu. Conductivitatea lor termică superioară asigură încălzirea uniformă și reduce consumul de energie. Rezistența ridicată a șocurilor termice minimizează riscul de fisurare în timpul schimbărilor rapide de temperatură, în timp ce stabilitatea lor chimică asigură puritatea metalului topit.
În concluzie, rețeta pentru creuzetele de carbură de siliciu de grafit este un amestec de materiale reglate fine care oferă un echilibru de conductivitate termică, rezistență la șoc termic și stabilitate chimică. Această compoziție le face indispensabile în domeniul metalurgiei, unde joacă un rol crucial în topirea și turnarea eficientă și fiabilă a metalelor.
Înțelegând componentele și procesul de fabricație al creuzetelor de grafit SIC, industriile pot lua alegeri în cunoștință de cauză pentru aplicațiile lor specifice, asigurând performanțe optime și longevitatea creuzelor lor. Pe măsură ce tehnologia avansează, sunt așteptate îmbunătățiri suplimentare ale rețetei și tehnicilor de fabricație ale creuzelor de grafit SIC, deschizând calea pentru procese metalurgice și mai eficiente și durabile.
Timpul post: 12-2024